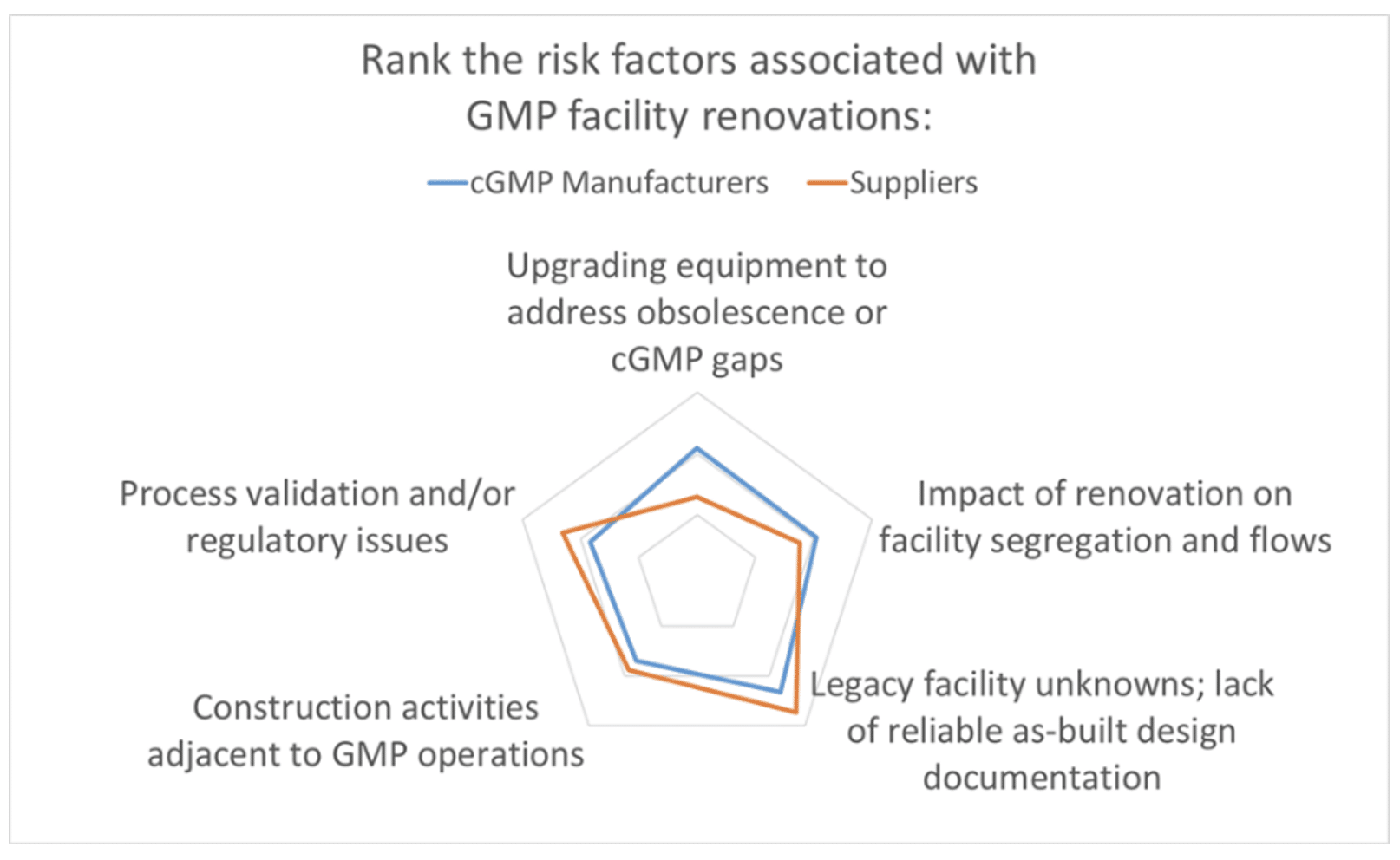
The results are in. As part of Facility Focus, an industry-wide survey of the life sciences industry conducted by Carroll Daniel Engineering, in partnership with INTERPHEX, we asked industry insiders – those in engineering and operations roles – to rank the risks that they encounter when renovating GMP space. The results were plotted on a radar chart to illustrate the relative weighting that pharma manufacturers and suppliers (mostly consulting engineers) placed on each risk factor.
The Devil You Don’t Know
Survey respondents ranked legacy facility unknowns and lack of reliable as-built design documentation as the leading risk associated with facility renovations. This was not surprising, as anyone with significant experience renovating manufacturing space will have a boatload of stories about projects that went south because of unanticipated issues with the existing space.
Many of the renovation projects we work on at are build-outs of acquired brownfield properties that were originally used for non-GMP purposes. Frequently, the architectural and MEP drawings of such buildings are incomplete, if they exist at all. It is advisable to execute a prospective engineering assessment of a property to determine its suitability for planned GMP operations before committing to its acquisition. Beyond that, some selective demolition and foundation core sampling/testing may be helpful to see what you are up against.
Even when the renovation is in a building that was originally built by the manufacturer, successive renovations and maintenance fit outs frequently leave the engineering documentation fragmented. Legacy piping, ductwork and electrical infrastructure may be abandoned in place, creating a congested mechanical space that is difficult to sort out. The true picture can only be pieced together with help from personnel who were involved in prior facility modifications – people who may or may not be available to assist the project.
Dealing with Unknowns
In any event, the design process for renovation projects typically starts with a field survey to document existing conditions at the site. Even when “as-built” design drawings are available, it is a good idea to verify the accuracy of these drawings during the site survey. At the end of the day, there is only so much you can do to protect yourself against the devil you don’t know. The best approach for GMP space is to commit the resources necessary to maintain drawings in an as-built state. However, many manufacturers fall short of this ideal, and when the renovation site is repurposed from non-GMP space – all bets are off. Lacking good documentation, the best you can do is gather as much data as you can in the beginning of the project and allow some reasonable slack in the schedule and budget to deal with the unknowns.
It’s Complicated
From the GMP manufacturer’s perspective, the other risks queried in the Facility Focus survey were equally challenging. After facility unknowns, the next highest risk identified by GMP manufacturers was upgrading equipment to address obsolescence or cGMP gaps. Suppliers (mostly engineering consultants) ranked this one lower – perhaps because this is an issue that is frequently addressed directly by the owner and equipment vendor – so GMP manufacturers may have a better appreciation of just how difficult this issue can be. The documentation typically provided with proprietary equipment is not intended to support future equipment modifications, and many equipment vendors are not geared for providing custom modifications of legacy equipment. New equipment solutions may be required if the original equipment cannot be modified. If the equipment in question is part of a validated manufacturing process, the task is even more complicated. The feasibility of equipment modifications is best addressed separately and before tackling a facility renovation.
Design to Comply
The remaining risk categories ranked highly in the survey all touch on requirements integral to current Good Manufacturing Practice. In order of survey ranking, these were:
- Impact of renovation on facility segregation and flows
- Process validation and/or regulatory issues
- Construction activities adjacent to GMP operations
Impacts of renovation on facility segregation and flows is a concern, since adding onto or repurposing space often disrupts the orderly movement of people, materials, equipment, product, and waste through the facility. Facility programming is not just focused on segregation and flows for new products or processes; it may require rethinking the movement of people and materials for legacy manufacturing within the facility as well.
It’s no surprise that Process validation and/or regulatory issues also ranked highly, since the central mission of a cGMP project is to ensure manufacturing operations can produce a compliant product. One unique aspect of working in GMP space is that the impact of validation – on cost and schedule – is a significant consideration in the development of the project scope and may place additional constraints on the project.
Finally, most of the renovation projects for which we are engaged involve construction adjacent to ongoing cGMP operations. Minimizing disruption to these operations is always a project mandate. It is essential that any atypical activities within the facility are properly segregated to prevent product contamination. Fortunately, this is a risk that can be mitigated through careful planning. We typically work closely with the owner, building contractors and construction manager to develop a detailed plan for segregating manufacturing space and utilities in operation, and for managing the separate and safe movement of people, equipment and materials to and from the construction zone.
The Facility Focus survey has provided insight into the minds of industry insiders – those who have their share of war stories from experience with cGMP projects in legacy facilities. Our intent at Carroll Daniel Engineering is to continue the dialog, culminating in an updated and improved Facility Focus program at the next INTERPHEX.