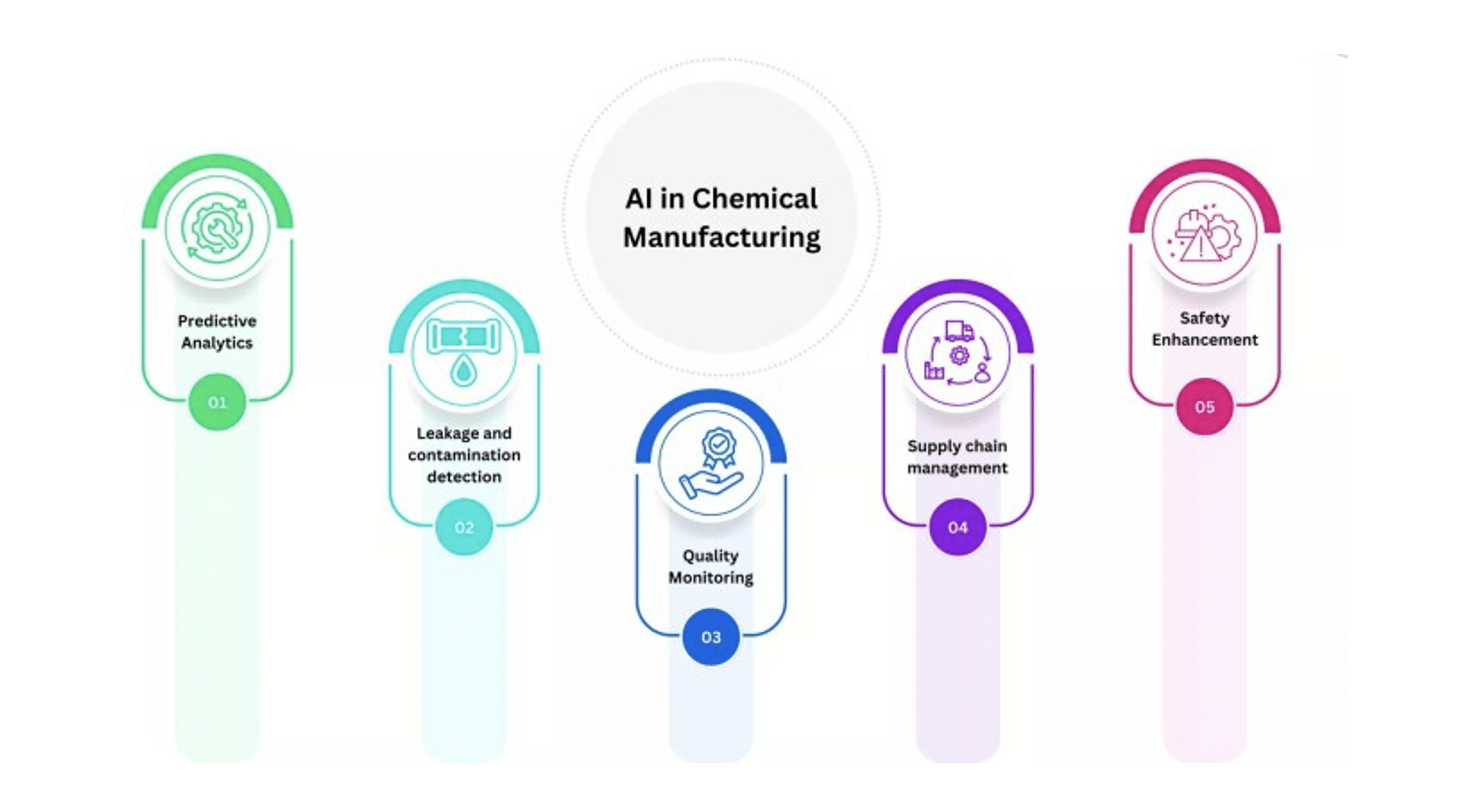
In process chemical manufacturing, precision, efficiency, safety, and quality are key factors in the plant’s success. Today, Machine Learning (ML) and Artificial Intelligence (AI) play increasingly significant roles in many aspects of the business, from research and development to manufacturing and supply chain management; while also reducing costs, improving efficiency, increasing safety, and enabling new product development. Despite some challenges, AI has the potential to reshape the chemical industry in the coming years. In this article, we will explore the practical applications of AI in process chemical manufacturing.
Many common issues encountered by chemical manufacturers can be addressed by AI, such as predicting downtimes on the production line (using tabular data collected from your machines), detecting leakages and contamination, root-cause analysis for unstable quality, low or fluctuating yields, and energy use optimization. Here are some specific examples of how AI is being used today to address some of these common issues:
Predictive analytics: Machine learning models can be trained on historical data from machines in chemical production and help predict how much raw material is needed for varied processes. These predictions can help flag any mismatches between recipe selection, dosing, and process conditions, avoiding any potential issues later in the process. Additionally, trained models can suggest future recipe refinement based on real-time quality data.
Leakage and contamination detection: Depending on the processes involved, with the right type of sensor installed, leakages and contamination can be easily detected. There are three different ways this problem can be approached:
- Analyzing images from CCTV or infrared cameras to detect leaks of hazardous materials, by training a model to identify changes in the color or consistency of chemicals or compounds, as well as the presence of unexpected vapors or fumes.
- If you have no collected historical data on pipeline conditions, you can use unsupervised machine learning to detect leaks by analyzing data from sensors that measure temperature, pressure, and flow. This method involves identifying abrupt changes in these variables, which could indicate a leak.
- If you have historical data on pipeline conditions, you can train a supervised machine learning model to predict leaks and contamination events. This method involves identifying patterns in the data that lead to leaks/contamination. The model can then be used to predict the likelihood of a leak or contamination event occurring in the future.
Quality Monitoring: ML and AI algorithms can be employed to monitor and maintain consistent product quality. Real-time data analysis helps identify deviations in chemical composition, ensuring adherence to specifications. If you are experiencing unstable quality in your products, an ML-powered root-cause analysis will help identify the problem. No matter how much data you have or how complex the process is, a machine learning algorithm can be trained on a variety of sources, including quality control data, supplier data, operator feedback, and environmental data. ML algorithms in addition to complex data analytics methods will be able to identify relationships between the variables that are contributing to quality problems.
Supply chain management: Machine Learning (ML) algorithms are highly capable of forecasting demand using your historical data, with 50% more accuracy compared to human forecasting, ensuring that essential chemicals are readily available [1]. The data gathered from your CRM and/or EPR system can provide valuable information regarding the demand for product or raw materials, and their correlation with time of year, location, shipping times, etc. across products, locations, and customers. Usually, the amount of data from these systems is overwhelming, and AI-powered forecasting is the best way to harness this data to generate accurate and actionable insights.
Safety Enhancement: AI-driven sensors and monitoring systems provide early detection of anomalies, such as leaks or temperature fluctuations. Immediate alerts enable a swift response to potential safety hazards. By analyzing historical safety data and failure records, ML algorithms can help identify anomalies in your plant and reduce the risk of accidents and enhance overall plant safety.
The use of AI in the chemical industry can offer a number of benefits, including reduced costs, improved efficiency, and increased safety. However, there are also some challenges to the implementation of AI, such as a lack of data, a shortage of AI skills, and uncertainty regarding ROI.
Carroll Daniel Engineering can help you overcome these challenges and reap the many benefits of AI. We provide a variety of AI-powered solutions that are tailored to the specific needs of the chemical industry. Our solutions can help you reduce downtime and increase OEE, optimize processes, improve quality control, and streamline supply chain management.